Ya estoy cortando las piezas y he comenzado por el panel de control que es lo mas sencillo en cuanto a carpintería se refiere, así voy cogiendo confianza.
Como no tengo sierra circular, solo la de calar, usé el viejo truco de colocar un listón como guía para el patín de la caladora. De esta forma conseguiría un corte recto sin problemas, pero como siempre, la realidad le hace a uno bajar a tierra. El corte no solo no seguía la línea que habia marcado, ademas se estaba biselando, y todo porque por alguna extraña razón, la hoja se doblaba hacia un lado y no seguía paralelismo con el patín… y eso que es una BOSCH.
Resulta que leyendo es.rec.bricolage he encontrado un post en el que dicen que las sierras de calar BOSCH tienen un problema de paralelismo entre el porta sierras y el patín, además de otros problemas como holgura vertical excesiva en el porta sierras, patín sin suela protectora que ralla lo que cortas y vibración excesiva.
Yo pensaba que tenia una buena sierra de calar pero veo que no es así… todos esos síntomas los he experimentado yo con mi sierra, pero pensaba que era por un manejo incorrecto por lo que obtenia esos resultados tan pobres.
Bueno, el caso es que mas o menos he conseguido darle forma al panel de control, he marcado los lugares donde iran colocados los joysticks y los botones (como no tengo impresora, ni la quiero, he tenido que tirar de escuadra, regla y geometría) y a la hora de hacer los agujeros me he dado cuenta de que tienen que ser de 28mm de diámetro y yo tengo brocas de pala de 25 y 30, la primera muy pequeña y la segunda demasiado grande. Al final opté por hacerlos de 30 aunque van con cierta holgura, pero hacer 20 agujeros de 25mm y agrandarlos a base de dremel es demasiado curro y no queda nada fino. Si me dedico a hacer esto en serie, ya me comprare la broca de 28mm. 🙂
![]() |
![]() |
![]() |
A continuación he hecho los rebajes interiores para que los joysticks queden mas altos y sobresalga un poco mas la palanca de mando, ya que al ponerlos por debajo del tablero del panel de control se pierden unos preciosos milímetros. Como no tengo fresadora, he usado la dremel. Cualquier trabajo con la dremel se tarda 5 veces mas que con la herramienta conveniente para el trabajo que se esté realizando, que siempre la hay. Creo que la dremel debería usarse solo para trabajos de precisión, por que para todo lo demás te eternizas.
Nota mental: Si se hace el fresado en 3 pasadas a distinta profundidad se tarda mucho menos que si se hace en 1 sola pasada.
Nota mental 2: Si rebajas primero el hueco con un formón y luego usas la fresadora, se tarda aun menos 🙂
![]() |
![]() |
Unos cuantos conectores fastón (fast on) hembra, que por cierto son carisimos para la mierdecilla que son, y unos cables uniendo las masas por un lado y por otro los que irán I-Pac. Se ordena todo un poquito y queda algo como esto:
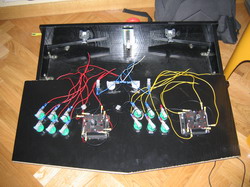
También he colocado unas bisagras invisibles para poder levantar la tapa cuando sea necesario y acceder al teclado y ratón del ordenador que estarán bajo los botones y los mandos.
![]() |
![]() |
Un par de botones para la emulación de pinball a los laterales, lo conectamos todo y agrupamos bien los cables para que no se enganchen. Ahora solo falta el cubrecantos de plástico que usaré en lugar de cinta de cantear o del “T molding” que usan las máquinas de los recreativos. La moldura en T no es fácil de encontrar en España y es mas rollo montarla por que hay que fresar los cantos haciendoles una pequeña ranura en el centro.
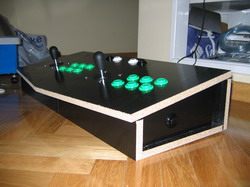
El cubrecantos de todos modos no lo colocaré hasta que solucione un par de detalles, uno es el arte que irá sobre el panel de control que en teoría ya me lo estan haciendo. Otro es una lámina de metacrilato de 2mm que irá encima de este para protegerlo de los arañazos y golpes que se producirán sin duda durante el uso.
Hola, espero no te moleste pero tu site me ha parecido tan bueno que he agregado un link en el mío para que mis visitantes conozcan el tuyo.
Saludos y felicitaciones.
¿Molestarme? Al contrario hombre, se trata de que esto lo lea la gente, así que encantado de que me enlaces.
Un saludo y gracias!